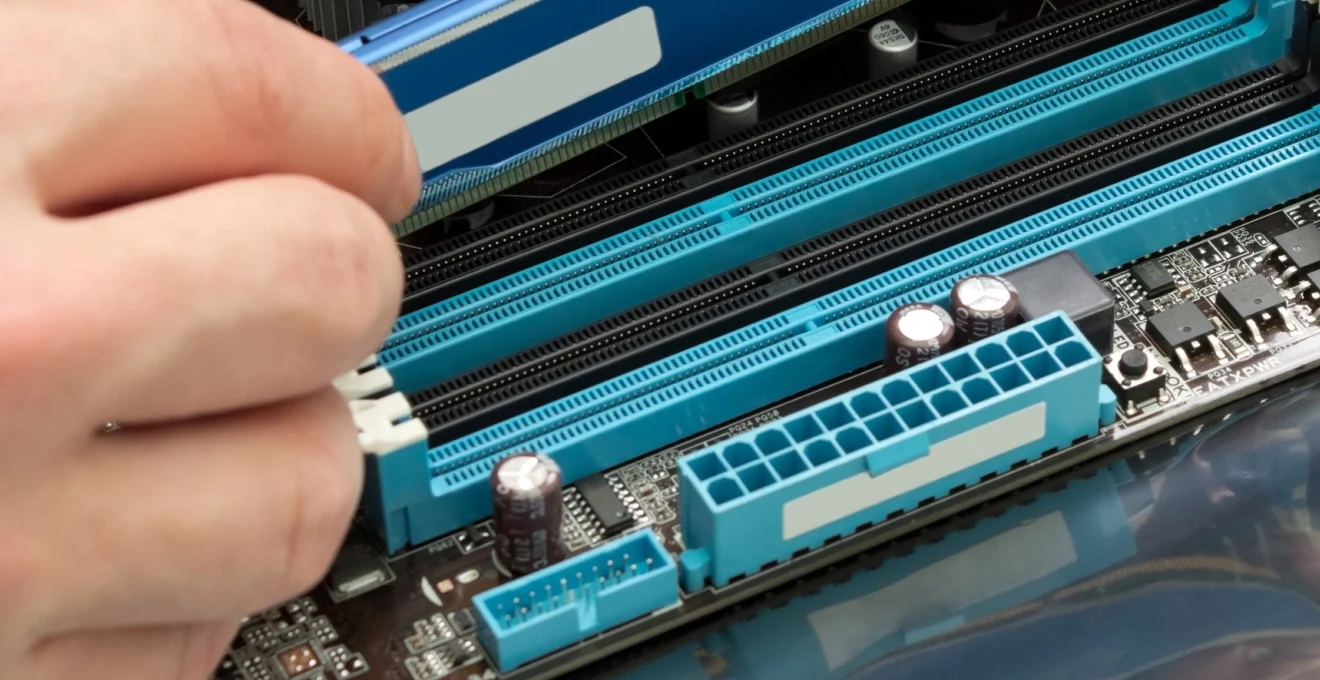
Electronic connectors serve as the critical interface between components and systems, playing a vital role in the functionality and reliability of modern devices. As technology advances, ensuring compatibility and optimizing performance in connectors becomes increasingly complex. From material selection to signal integrity, environmental considerations to compliance testing, mastering the intricacies of connector design and implementation is essential for engineers and manufacturers alike.
The world of electronic connectors is vast and diverse, encompassing a wide range of types of connectors tailored to specific applications and industries. Whether you're working on consumer electronics, industrial machinery, or cutting-edge aerospace systems, understanding the key factors that influence connector performance is crucial for creating robust and efficient designs.
Electrical and mechanical interface standards for connectors
Standardization plays a pivotal role in ensuring compatibility across different manufacturers and applications. Industry standards define the electrical and mechanical specifications that connectors must adhere to, facilitating interoperability and simplifying design processes. Some of the most widely recognized standards include:
- USB (Universal Serial Bus)
- HDMI (High-Definition Multimedia Interface)
- Ethernet (RJ45)
- PCIe (Peripheral Component Interconnect Express)
- MIL-DTL-38999 (Military Standard)
These standards specify crucial parameters such as pin configurations, signal assignments, mechanical dimensions, and electrical characteristics. Adhering to these standards ensures that connectors from different sources can work seamlessly together, reducing compatibility issues and streamlining system integration.
When selecting connectors for your application, it's essential to consider not only the current requirements but also future scalability. For instance, the USB standard has evolved from USB 1.0 to the latest USB4, with each iteration offering higher data transfer rates and improved power delivery capabilities. Choosing connectors that comply with forward-looking standards can future-proof your designs and extend the lifespan of your products.
Material selection for optimal connector performance
The choice of materials used in connector construction significantly impacts their performance, durability, and reliability. Each component of a connector, from the conductive elements to the insulating body and shielding materials, requires careful consideration to meet the specific demands of the application.
Conductive materials: copper alloys vs. gold plating
The heart of any electrical connector lies in its conductive components. Copper alloys, such as brass and phosphor bronze, are commonly used due to their excellent electrical conductivity and mechanical properties. However, these base metals are often plated with more noble metals to enhance performance and durability.
Gold plating is widely regarded as the gold standard (pun intended) for high-reliability connections. Its excellent conductivity, corrosion resistance, and low contact resistance make it ideal for applications where signal integrity is paramount. However, gold plating comes at a premium cost.
Insulating materials: comparing PTFE, PVC, and silicone
The insulating materials used in connectors play a crucial role in maintaining signal integrity and providing mechanical support. Three commonly used materials are:
- PTFE (Polytetrafluoroethylene): Known for its excellent dielectric properties and high-temperature resistance
- PVC (Polyvinyl Chloride): Cost-effective and versatile, suitable for many general-purpose applications
- Silicone: Offers good flexibility and temperature resistance, ideal for automotive and industrial uses
When selecting insulating materials, consider factors such as operating temperature range, chemical resistance, and dielectric strength. For instance, PTFE excels in high-frequency applications due to its low dielectric constant and dissipation factor, making it the material of choice for RF connectors and high-speed digital interfaces.
Shielding materials: EMI/RFI considerations
In today's electromagnetically noisy environments, effective shielding is crucial for maintaining signal integrity and preventing interference. Connector shielding typically involves the use of conductive materials to create a Faraday cage around the signal-carrying components.
Common shielding materials include:
- Aluminum: Lightweight and cost-effective
- Copper: Excellent conductivity but heavier and more expensive
- Nickel-plated materials: Good balance of performance and cost
The choice of shielding material depends on the level of protection required and the specific EMI/RFI challenges in the application environment. For instance, aerospace and military applications often require more robust shielding solutions to withstand extreme electromagnetic conditions.
Signal integrity in high-speed connectors
As data rates continue to increase in modern electronic systems, maintaining signal integrity becomes increasingly challenging. High-speed connectors must be designed and implemented with careful consideration of various factors that can degrade signal quality.
Impedance matching techniques for differential pairs
Impedance matching is critical for minimizing signal reflections and ensuring efficient power transfer in high-speed data transmission. For differential signaling, which is commonly used in protocols like USB 3.0 and PCIe, maintaining consistent differential impedance throughout the connector is essential.
Techniques for achieving proper impedance matching include:
- Precise control of conductor geometry and spacing
- Use of impedance-controlled PCB layouts
- Implementation of ground planes and reference planes
- Careful selection of dielectric materials
Engineers often use specialized simulation tools to optimize connector designs for impedance matching, ensuring that the characteristic impedance remains consistent across the entire signal path.
Crosstalk mitigation strategies in dense connector designs
As connector pin densities increase to accommodate more signals in smaller form factors, the risk of crosstalk between adjacent signal pairs also rises. Crosstalk can lead to signal degradation and increased bit error rates in high-speed data transmission.
Effective crosstalk mitigation strategies include:
- Optimizing pin assignments to separate high-speed differential pairs
- Implementing ground shields between signal pairs
- Using advanced PCB layout techniques like serpentine routing
- Employing specialized connector designs with integrated shielding structures
By carefully considering these factors in the connector design phase, engineers can significantly reduce crosstalk and improve overall signal integrity in dense, high-speed applications.
Insertion loss and return loss optimization
Insertion loss and return loss are crucial parameters in assessing the performance of high-speed connectors. Insertion loss refers to the attenuation of the signal as it passes through the connector, while return loss measures the amount of signal reflected back due to impedance mismatches.
Environmental factors affecting connector reliability
Connectors often operate in challenging environments, exposed to various physical and chemical stressors. Understanding and addressing these environmental factors is crucial for ensuring long-term reliability and performance.
IP ratings for moisture and dust protection
Ingress Protection (IP) ratings provide a standardized method for specifying the environmental protection offered by electrical enclosures. For connectors, IP ratings are particularly important in applications where exposure to moisture or particulates is a concern.
The IP rating system uses a two-digit code:
- The first digit (0-6) indicates protection against solid objects and dust
- The second digit (0-9) indicates protection against liquids
For example, an IP67-rated connector is fully protected against dust ingress and can withstand temporary immersion in water. When selecting connectors for outdoor or industrial applications, carefully consider the required IP rating based on the expected environmental conditions.
Thermal management in high-current applications
High-current applications, such as power distribution systems or electric vehicle charging, pose unique challenges for connector design. As current flow increases, so does heat generation, which can lead to reduced performance, accelerated aging, and even failure if not properly managed.
Effective thermal management strategies for high-current connectors include:
- Using materials with high thermal conductivity for connector bodies and contacts
- Implementing larger contact surface areas to reduce current density
- Incorporating heat sink features into connector designs
- Ensuring proper airflow and cooling in the overall system design
By addressing thermal considerations early in the design process, engineers can create connectors that maintain reliable performance even under high-current conditions.
Vibration and shock resistance in automotive connectors
Automotive applications subject connectors to constant vibration and occasional shock loads, which can lead to fretting corrosion, loosening of connections, and eventual failure if not properly addressed. Designing connectors for vibration and shock resistance requires careful consideration of both materials and mechanical design.
Compliance testing and certification processes
Ensuring that connectors meet industry standards and regulatory requirements is essential for product safety, reliability, and market acceptance. Compliance testing and certification processes provide a structured approach to validating connector performance and quality.
IEC 60512 connector testing standards
The International Electrotechnical Commission (IEC) 60512 series of standards provides a comprehensive framework for testing electromechanical components, including connectors. These standards cover a wide range of tests, including:
- Electrical characteristics (contact resistance, insulation resistance, etc.)
- Mechanical properties (insertion and withdrawal forces, durability, etc.)
- Climatic tests (temperature cycling, humidity, salt spray, etc.)
- Environmental tests (vibration, shock, IP rating verification, etc.)
Adhering to these standardized testing procedures ensures that connectors meet minimum performance requirements and allows for meaningful comparisons between different products.
UL recognition vs. listing for electronic connectors
Underwriters Laboratories (UL) certification is widely recognized in North America and globally as a mark of product safety and quality. For electronic connectors, there are two main types of UL certification:
- UL Recognition: Applies to components intended for use in other end products
- UL Listing: Applies to complete products ready for end-user installation
Most connectors fall under the UL Recognition program, as they are typically integrated into larger systems or products. UL Recognition involves rigorous testing of the connector's electrical, thermal, and mechanical properties to ensure it meets safety standards when used within its specified parameters.
Military-spec (MIL-STD) compliance for harsh environments
Military and aerospace applications often require connectors that can withstand extreme conditions and meet stringent reliability standards. Military Standard (MIL-STD) specifications provide a set of rigorous requirements for connectors used in these demanding environments.
Key MIL-STD specifications for connectors include:
- MIL-DTL-38999: Circular connectors for aerospace applications
- MIL-DTL-83513: Micro-miniature connectors
- MIL-DTL-55302: Printed circuit board connectors
Compliance with these standards involves extensive testing for factors such as vibration resistance, shock tolerance, corrosion resistance, and performance under extreme temperatures. MIL-SPEC compliant connectors often find use in critical applications beyond military and aerospace, where utmost reliability is required.
Future trends in connector technology
The field of connector technology is continuously evolving to meet the demands of emerging applications and industries. Several key trends are shaping the future of connector design and implementation.
Miniaturization: micro and nano connector designs
As electronic devices continue to shrink in size while increasing in functionality, the demand for smaller, higher-density connectors grows. Micro and nano connector designs push the boundaries of manufacturing capabilities, offering unprecedented levels of miniaturization.
Key challenges in micro and nano connector development include:
- Maintaining signal integrity in tightly packed configurations
- Ensuring reliable contacts with reduced surface areas
- Developing new manufacturing processes for ultra-small components
- Addressing handling and assembly challenges in production
Despite these challenges, miniaturized connectors are enabling new possibilities in wearable technology, medical devices, and other space-constrained applications.
High-power connectors for electric vehicle charging
The rapid growth of the electric vehicle (EV) market is driving innovation in high-power connector design. EV charging connectors must handle increasingly high currents and voltages while ensuring safety, ease of use, and long-term reliability.
Emerging trends in EV charging connectors include:
- Development of standardized fast-charging interfaces
- Implementation of intelligent charging systems with integrated data communication
- Enhanced cooling solutions for ultra-fast charging capabilities
- Integration of safety features like automatic power cut-off and ground fault detection
As EV adoption accelerates, we can expect continued innovation in high-power connector technology to support faster charging times and improved user experiences.
Optical interconnects for data center applications
The ever-increasing demand for data center bandwidth is pushing the limits of traditional copper-based interconnects. Optical interconnects, using fiber optic technology, offer significant advantages in terms of data rates, signal integrity over long distances, and reduced power consumption.
As data center architectures evolve to meet the demands of cloud computing, artificial intelligence, and 5G networks, optical interconnects will play an increasingly crucial role in enabling high-speed, high-bandwidth communications.
The transition from copper-based interconnects to optical solutions in data centers is not without challenges. Engineers must grapple with issues such as thermal management in high-density optical connectors, ensuring signal integrity across multiple optical interfaces, and developing cost-effective manufacturing processes for large-scale deployment. However, the potential benefits in terms of bandwidth, latency reduction, and energy efficiency make optical interconnects a compelling solution for next-generation data center infrastructure.
As we look to the future of connector technology, it's clear that innovation will continue to drive advancements across various industries and applications. From the tiniest micro-connectors in wearable devices to high-power charging interfaces for electric vehicles and cutting-edge optical interconnects in data centers, the field of connector design and implementation remains dynamic and full of opportunities for further development.