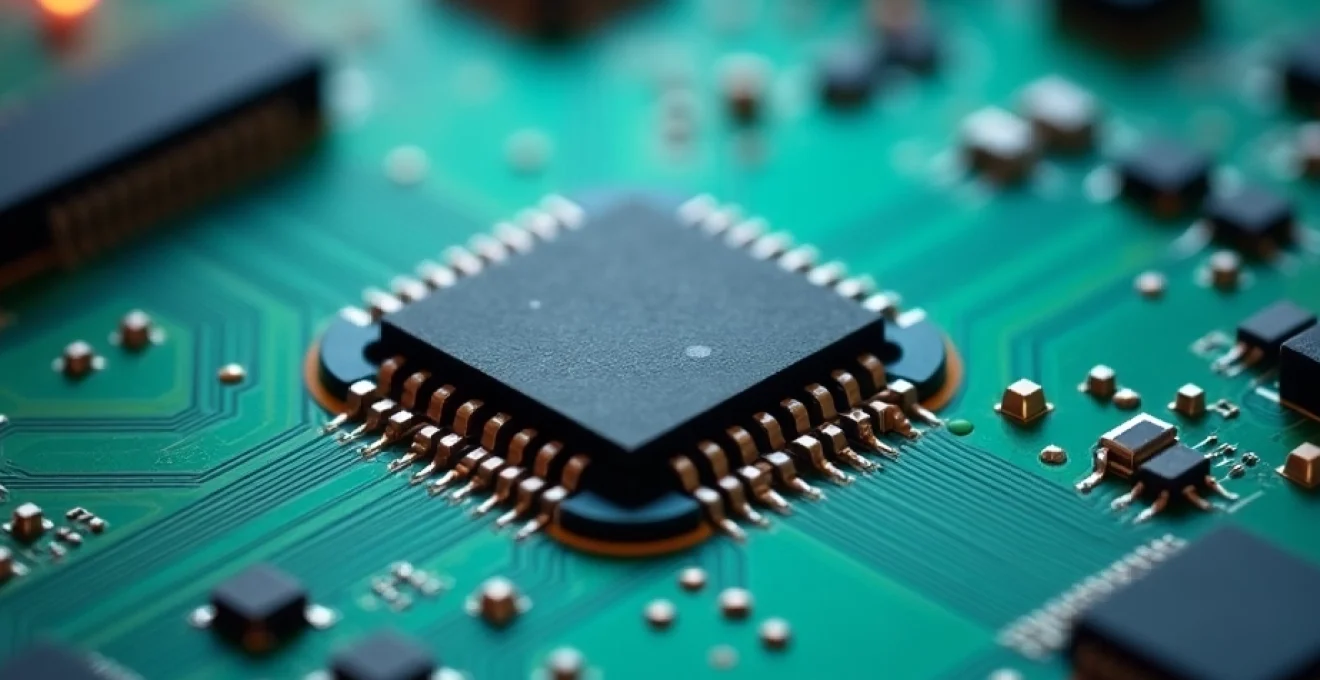
Electrostatic discharge (ESD) poses a significant threat to electronic devices, potentially causing irreversible damage and costly failures. As our reliance on sensitive electronic components grows, so does the importance of implementing robust ESD protection strategies. From conductive polymers to advanced shielding techniques, the world of ESD protection is evolving rapidly to meet the demands of modern electronics.
Understanding electrostatic discharge (ESD) and its impact on electronics
Electrostatic discharge occurs when two objects with different electrical potentials come into contact, resulting in a sudden flow of electricity. In the realm of electronics, even a minuscule ESD event can wreak havoc on delicate circuitry. The semiconductor industry is particularly vulnerable, with ESD-related failures accounting for a significant portion of device returns and field failures.
The impact of ESD on electronics can range from subtle performance degradation to catastrophic failure. Gate oxide breakdown in MOSFETs, junction burnout in diodes, and metal melt in interconnects are just a few examples of the damage ESD can inflict. As device geometries continue to shrink and operating voltages decrease, the sensitivity to ESD events increases exponentially.
To combat this threat, the electronics industry has developed a multifaceted approach to ESD protection. This encompasses everything from specialized materials and circuit design techniques to rigorous handling procedures and manufacturing controls. By implementing comprehensive ESD protection strategies, companies can significantly reduce the risk of ESD-related failures and improve product reliability.
Key ESD protection materials and their properties
The foundation of effective ESD protection lies in the materials used to shield, dissipate, or neutralize static charges. These materials range from conductive polymers to sophisticated metal-based shielding solutions. Each type of material offers unique properties that make it suitable for specific applications within the ESD protection landscape.
Conductive polymers: PEDOT:PSS and polyaniline
Conductive polymers represent a revolutionary class of materials that combine the flexibility and processability of plastics with the electrical conductivity of metals. Two prominent examples in the field of ESD protection are PEDOT:PSS (poly(3,4-thylenedioxythiophene) polystyrene sulfonate) and polyaniline.
PEDOT:PSS has gained significant traction due to its excellent conductivity, transparency, and stability. It's commonly used in antistatic coatings for displays, flexible electronics, and touch panels. Polyaniline, on the other hand, offers tunable conductivity and can be easily synthesized, making it a versatile option for ESD-safe packaging and coatings.
These conductive polymers work by providing a low-resistance path for static charges to dissipate, preventing the buildup of potentially damaging voltages. Their ability to be processed into thin films and coatings makes them particularly useful in applications where traditional metal-based solutions might be impractical.
Metal-based shielding: copper and aluminum foils
When it comes to robust ESD protection, metal-based shielding remains a go-to solution for many applications. Copper and aluminum foils are widely used due to their excellent conductivity and shielding effectiveness. These materials work on the principle of the Faraday cage, effectively blocking external electric fields and providing a safe haven for sensitive electronics.
Copper foil, with its superior conductivity, is often used in high-performance ESD shielding applications. It's particularly effective in creating EMI/RFI shields for electronic enclosures and PCB designs. Aluminum foil, while slightly less conductive than copper, offers the advantage of being lighter and more cost-effective, making it suitable for large-scale ESD protection in packaging and transportation.
The effectiveness of metal-based shielding is largely dependent on the thickness of the material and the quality of grounding. Proper implementation can provide protection against ESD events up to several kilovolts, making these materials indispensable in high-risk environments.
Carbon-based materials: graphene and carbon nanotubes
The realm of carbon-based materials has opened up exciting new possibilities for ESD protection. Graphene and carbon nanotubes (CNTs) are at the forefront of this innovation, offering exceptional electrical properties in ultra-thin, lightweight form factors.
Graphene, a single layer of carbon atoms arranged in a hexagonal lattice, boasts remarkable conductivity and strength. When incorporated into composites or coatings, graphene can provide effective ESD protection while maintaining transparency and flexibility. This makes it an attractive option for touchscreens, flexible electronics, and wearable devices.
Carbon nanotubes, with their unique tubular structure, offer high aspect ratios and excellent electrical conductivity. CNT-based composites can be tailored to provide specific levels of conductivity, making them versatile for various ESD protection applications. From conductive adhesives to ESD-safe fabrics, CNTs are pushing the boundaries of what's possible in static control.
Antistatic coatings: quaternary ammonium compounds
Quaternary ammonium compounds (QACs) play a crucial role in creating antistatic surfaces that prevent the accumulation of static charges. These ionic compounds work by forming a thin, conductive layer on the surface of materials, allowing charges to dissipate harmlessly.
QACs are particularly useful in creating antistatic coatings for plastics, which are inherently insulative and prone to static buildup. By applying a QAC-based coating, manufacturers can transform common plastics into ESD-safe materials suitable for packaging, trays, and containers used in electronics manufacturing and transportation.
The effectiveness of QAC coatings can be influenced by environmental factors such as humidity and temperature. However, their ability to provide long-lasting antistatic properties without significantly altering the base material's characteristics makes them a valuable tool in the ESD protection arsenal.
ESD protection strategies for PCB design
Effective ESD protection extends beyond materials to encompass strategic design choices in printed circuit boards (PCBs). By incorporating ESD protection elements directly into the PCB layout, designers can create robust systems capable of withstanding multiple ESD events without failure.
TVS diodes and their role in transient voltage suppression
Transient Voltage Suppression (TVS) diodes are semiconductor devices specifically designed to protect sensitive electronics from voltage spikes, including those caused by ESD events. These diodes act as a "safety valve" for electrical circuits, quickly diverting excess energy away from vulnerable components.
When implementing TVS diodes in PCB designs, several factors must be considered:
- Placement: TVS diodes should be positioned as close as possible to the potential entry points of ESD, such as connectors or exposed traces.
- Sizing: The breakdown voltage and clamping voltage of the TVS diode must be carefully selected to match the protection requirements of the circuit.
- Response time: High-speed TVS diodes are crucial for protecting against the rapid voltage changes characteristic of ESD events.
- Capacitance: For high-frequency applications, low-capacitance TVS diodes are essential to minimize signal distortion.
By strategically incorporating TVS diodes into PCB designs, engineers can create a first line of defense against ESD, significantly enhancing the overall reliability of electronic systems.
Implementing ESD protection rings in IC layout
ESD protection rings are a critical design element in integrated circuit (IC) layouts, providing a dedicated path for ESD currents to flow around sensitive core circuitry. These rings typically consist of a continuous metal trace surrounding the IC's functional blocks, connected to dedicated ESD protection structures.
The effectiveness of ESD protection rings depends on several design considerations:
- Width and resistance: The ring must be wide enough to handle high current flows without significant voltage drops.
- Connectivity: Ensuring proper connections between the ring and all I/O pads is crucial for comprehensive protection.
- Isolation: The ring should be isolated from noise-sensitive circuits to prevent interference.
- Symmetry: A symmetrical layout helps distribute ESD currents evenly, preventing localized damage.
By carefully implementing ESD protection rings, IC designers can create a robust barrier against ESD events, significantly improving the longevity and reliability of their devices.
Grounding techniques: star point and mesh grounding
Proper grounding is fundamental to effective ESD protection in PCB design. Two common grounding techniques are star point grounding and mesh grounding, each with its own advantages and applications.
Star point grounding involves connecting all ground points to a single, central location. This approach minimizes ground loops and can be highly effective in reducing noise in analog circuits. However, it may not be suitable for high-frequency applications due to the potential for long ground return paths.
Mesh grounding, on the other hand, creates a network of interconnected ground planes. This technique is particularly effective for high-frequency designs and large PCBs, as it provides multiple low-impedance paths for current flow. The downside is the increased complexity in layout and potential for ground loops if not implemented correctly.
Choosing the right grounding technique depends on factors such as circuit complexity, operating frequency, and the specific ESD protection requirements of the design. In some cases, a hybrid approach combining elements of both star point and mesh grounding may provide the optimal solution.
Esd-safe PCB materials: FR-4 vs. High-Tg laminates
The choice of PCB substrate material plays a crucial role in determining a board's overall ESD resistance. While traditional FR-4 (Flame Retardant 4) remains a popular choice due to its cost-effectiveness and well-understood properties, high-Tg (glass transition temperature) laminates are gaining traction in applications requiring enhanced ESD protection.
FR-4 offers reasonable ESD performance for many applications, but its limitations become apparent in high-temperature or high-frequency environments. High-Tg laminates, such as polyimide or ceramics, offer superior thermal stability and electrical performance, making them ideal for demanding ESD protection scenarios.
When selecting PCB materials for ESD-sensitive designs, consider the following factors:
- Operating temperature range
- Frequency requirements
- Dimensional stability
- Moisture absorption
- Dielectric constant and loss tangent
By carefully weighing these factors and selecting the appropriate PCB material, designers can create a solid foundation for robust ESD protection in their electronic systems.
Evaluating ESD protection effectiveness: testing methods and standards
Ensuring the effectiveness of ESD protection measures requires rigorous testing and adherence to established standards. The electronics industry has developed several standardized test methods to evaluate the ESD susceptibility of devices and the performance of protection strategies.
Human body model (HBM) testing per ANSI/ESDA/JEDEC JS-001
The Human Body Model (HBM) test is one of the most widely used methods for assessing ESD susceptibility. It simulates the discharge that occurs when a charged human touches an electronic device. The ANSI/ESDA/JEDEC JS-001 standard provides a comprehensive framework for conducting HBM tests, ensuring consistency and comparability across the industry.
Key aspects of HBM testing include:
- Voltage levels: Typically ranging from 100V to 8kV
- Waveform characteristics: Specific rise time and decay parameters
- Pin combinations: Testing various pin-to-pin and pin-to-ground scenarios
- Failure criteria: Defining what constitutes a device failure post-ESD stress
By subjecting devices to standardized HBM tests, manufacturers can gauge the effectiveness of their ESD protection measures and make informed decisions about design improvements or additional safeguards.
Machine model (MM) and charged device model (CDM) tests
While the HBM test remains prevalent, the Machine Model (MM) and Charged Device Model (CDM) tests address other important ESD scenarios encountered in real-world environments.
The Machine Model simulates ESD events that occur when charged equipment or tools come into contact with electronic devices. Although less commonly used today, MM testing can still provide valuable insights for certain industrial applications.
The Charged Device Model, on the other hand, has gained significant importance in recent years. It simulates the rapid discharge that occurs when a charged device comes into contact with a grounded object. CDM events are particularly relevant in automated manufacturing processes and can cause damage even to devices with robust HBM protection.
Both MM and CDM tests have their own standardized procedures and voltage levels, allowing for comprehensive evaluation of ESD protection strategies across different discharge scenarios.
IEC 61000-4-2 compliance for consumer electronics
For consumer electronics and other finished products, compliance with the IEC 61000-4-2 standard is often mandatory. This standard defines test methods for evaluating the immunity of equipment to ESD events that might occur during normal use.
IEC 61000-4-2 testing involves two main types of discharges:
- Contact discharge: Direct application of the ESD gun to conductive surfaces
- Air discharge: Approaching the ESD gun to insulative surfaces until a discharge occurs
The standard specifies multiple test levels, with voltages ranging from 2kV to 15kV, allowing manufacturers to certify their products for different operating environments and user expectations.
Compliance with IEC 61000-4-2 not only ensures product reliability but also plays a crucial role in meeting regulatory requirements for market access in many countries.
Advanced ESD protection technologies for sensitive components
As electronic components become increasingly sensitive to ESD events, advanced protection technologies are emerging to meet these challenges. These cutting-edge solutions often combine multiple approaches to create comprehensive ESD protection systems.
One promising area of development is the use of nanocomposite materials that integrate conductive nanoparticles into polymer matrices. These materials can provide tunable conductivity and ESD protection while maintaining the mechanical properties of the base polymer. For instance, carbon nanotube-infused epoxies are being explored for creating ESD-safe adhesives and encapsulants for sensitive semiconductor packages.
Another innovative approach involves the development of "smart" ESD protection circuits that can adapt their response based on the severity of the ESD event. These circuits use advanced sensing and switching technologies to provide optimal protection across a wide range of discharge scenarios, minimizing the impact on normal device operation.
Additionally, the integration of ESD protection directly into semiconductor processes is gaining traction. By incorporating specialized ESD protection structures at the transistor level, chip manufacturers can create inherently ESD-resistant devices without relying solely on external protection components.
Implementing ESD control programs in manufacturing environments
Effective ESD protection extends beyond materials and circuit design to encompass comprehensive control programs in manufacturing environments. These programs are essential for maintaining a static-safe workspace and ensuring the reliability of produced electronic devices.
Esd-safe workstations: wrist straps and conductive flooring
Creating ESD-safe workstations is a fundamental aspect of any ESD control program. Key elements include:
- Wrist straps: These provide a direct connection between the operator and ground, preventing charge accumulation on the human body.
- Conductive flooring: ESD-dissipative floor materials help prevent charge buildup as personnel move around the workspace.
- Grounded work surfaces: Conductive or dissipative mats on workbenches provide a safe surface for handling sensitive components.
- ESD-safe chairs: Specially designed chairs with conductive materials prevent charge accumulation
Ionization systems for neutralizing static charges
Ionization systems play a crucial role in neutralizing static charges in manufacturing environments where ESD-sensitive components are handled. These systems work by emitting a balanced stream of positive and negative ions into the air, effectively neutralizing any static buildup on surfaces or objects.
Key components of effective ionization systems include:
- Overhead ionizers: Mounted above workstations to provide broad coverage
- Benchtop ionizers: Targeted ionization for specific work areas
- Compressed air ionizers: For cleaning and neutralizing charges in hard-to-reach areas
- Ionizing blowers: For larger spaces or conveyor systems
When implementing ionization systems, it's important to consider factors such as air flow, ion balance, and decay time to ensure optimal performance. Regular maintenance and calibration of ionizers are essential to maintain their effectiveness in neutralizing static charges.
ESD packaging solutions: faraday cages and dissipative bags
Proper packaging is critical for protecting ESD-sensitive components during storage and transportation. Two key solutions in this area are Faraday cages and dissipative bags.
Faraday cages, named after physicist Michael Faraday, are enclosures made of conductive materials that block external electric fields. In ESD protection, Faraday cage principles are applied to create shielding containers and packaging that protect sensitive electronics from external static charges.
Dissipative bags, on the other hand, are designed to slowly and safely discharge static buildup. These bags are typically made from materials with a surface resistivity between 1 x 10^5 and 1 x 10^12 ohms per square, allowing charges to dissipate without causing sudden discharges that could damage components.
When selecting ESD packaging solutions, consider factors such as:
- The sensitivity of the components being protected
- Environmental conditions during storage and shipping
- Compatibility with automated handling systems
- Reusability and cost-effectiveness
Personnel training and certification: ESD association programs
A crucial aspect of implementing effective ESD control programs is ensuring that all personnel working with ESD-sensitive components are properly trained and certified. The ESD Association (ESDA) offers a range of training and certification programs designed to educate workers on ESD risks and best practices.
Key ESDA certification programs include:
- Certified ESD Program Manager: For individuals responsible for developing and managing ESD control programs
- Certified ESD Control Technician: For those who implement and maintain ESD control measures
- ESD Certified Professional: A comprehensive certification for ESD specialists
These programs cover topics such as ESD physics, control methods, standards compliance, and auditing techniques. By investing in personnel training and certification, organizations can significantly reduce the risk of ESD-related failures and improve overall product quality.
Regular refresher courses and updates on new ESD protection technologies and standards should also be part of ongoing training efforts to maintain a high level of ESD awareness and compliance throughout the organization.